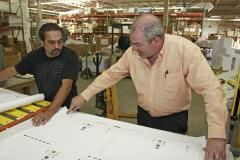
Printers and people in the business rely on the expertise of Dave Theriault at Elite for answers to all their technical envelope questions. Dave has been in the business of making and printing envelopes for over twenty years.
Have you ever had a question and either didn't know where to find the answer or were too afraid to ask? If so, you've come to the right place.
As the name would suggest, this section is a compilation of answers to the questions our clients commonly ask. Envelope manufacturing can be confusing, even to experienced graphic arts professionals. We've tried to provide as many details as possible in a clear, concise fashion. Just start by following one of the links below.
- At what resolution should I save my photos and graphics?
- How do I go about getting an estimate from you?
- How long does it take for you to complete my order?
- Is white considered a printing color?
- Tips on how to save your design files
- What do you need from me to do a converting job?
- What file format should I use when submitting my electronic document for printing?
- What is a "proof"?
- What is the Pantone Matching System?
- What is the difference between Flexo and Offset Printing?
- What type of products and services do you provide?
- Why are there overruns on custom jobs?
- Why do the printed colors look different from the colors on my screen?
- What's the best way to print an envelope?
-
At what resolution should I save my photos and graphics?
Resolution should be set to 300 dpi.
Pictures and graphics pulled from the internet are often low resolution, typically 72 dpi or 96 dpi. Avoid these graphics, as they will appear pixilated and blocky when printed.
Also note that you should save all photos in CMYK mode, not RGB mode when possible. Images saved in RGB mode may not print properly. If you are unable to save your image in CYMK mode, please let us know.
-
How do I go about getting an estimate from you?
Well, since you are here, we would suggest you use our online estimate request form. Otherwise, just give us a call at 781 961 1800 or fax us a request at 781 961 1805. We'll always respond within 24 hours; most of the time same day. If you need it sooner, just tell us and we'll do our best.
-
How long does it take for you to complete my order?
Most manufactured or "make" jobs will take 5-10 business days. Anything we have in stock that doesn't require printing is usually shipped within 48 hours or less. Some items can take longer depending on their complexity. Just let us know what you need and we'll generally make it happen.
-
Is white considered a printing color?
Not typically. Because white is the default color of paper, it is simply recognized as the absence of any ink. However, when using colored paper, white ink may be used if any text or graphic requires it.
-
Tips on how to save your design files
Make them print ready and acceptable for us to print.
COREL DRAW:
Saving your Corel Draw file as an Adobe Illustrator EPS
• Embed all Images
• Convert all your text/copy to outline fonts
• Export as Illustrator EPSFREEHAND:
• Embed all Images
• Convert all your text/copy to paths
• Export as Illustrator EPS or PDFPAGEMAKER:
Saving your PageMaker file as an EPS
• Embed all Images
• Convert all your text/copy to outline fonts
• Export your file as an EPS using the below settings:
Postscript Level 2
CMYK Mode
TIFF format and
BinaryPUBLISHER:
You will need to have the full version of Adobe Acrobat PDF. If you don’t please download and use our Adobe Job Ready Program. If you do have the full version of Adobe Acrobat PDF please follow the steps below.
Under File, Print, select Adobe PDF writer
Under Properties select Press Quality and Save your PDF -
What do you need from me to do a converting job?
Converting jobs can be complicated but following the following simple steps will ensure that all goes smoothly.
The first step is to give us the size and tell us what size sheet you'll be printing it on. We'll send you a print layout showing you how the job should be positioned for printing. You'll need to print in the exact position indicated on the layout.
Press sheets must be the same size as the supplied layout. Do not make any changes without advising us.
Make 3 spotter sheets for every 1,000 printed sheets. Spotter sheets must be kept separate, clearly marked and on top of the order.
Do not print more than one copy lot on a press sheet unless the job is quoted that way. This can become confusing and result in mismatched packaging.
When packaging your sheets to send to us, separate and clearly mark different lots.
Grain of the paper must run in the direction indicated on our layout.
If you looking to convert stock which is coated on both sides, we must see a sample of the stock beforehand in order to ensure that folding and gluing will not be a problem.
There must be a 1/8" bleed over any edge or fold of the envelope. All envelope converting involves up to 1/16" variation in cutting and folding. It is not possible to have a bleed lay exactly on the score or fold line 100% of the time.
Medium to heavy coverage jobs must be varnished to minimize marking. Solid coverages within a job should be spot varnished for the same reason.
If the envelope is printed with full ink coverage, you will need a "no print area" sample from us for glue areas.
Always call for spoilage requirements if they are not indicated on your quote or if specifications have changed at all from the original quote.
Sheets must come to us fully jogged and should be on a skid (not in cartons) with the number of sheets clearly marked on each skid.
Please return our layout with the job.
-
What file format should I use when submitting my electronic document for printing?
PDF (Portable Document Format) is the most common and preferred file format for submitting digital documents. With the installation of a PDF print driver on your computer, virtually any program can generate a PDF file suitable for printing. Both commercial and free PDF print drivers are available online for download from different sources.
-
What is a "proof"?
A proof is a way of ensuring that we have set your type and layout accurately and that everything is positioned according to your requirements. Typically, we will produce a proof which will be sent to you online or laser printed for your review.
If we need to correct something or if you've had second thoughts, you can request a second proof until we all agree it's ready to print.
-
What is the Pantone Matching System?
The Pantone Matching System (PMS) is a color reproduction standard in which colors all across the spectrum are each identified by a unique, independent number. The use of PMS allows us to precisely match colors and maintain color consistency throughout the printing process.
-
What is the difference between Flexo and Offset Printing?
Flexo and Offset are the two most common print processes for envelopes. "Flexo" is short for Flexographic which means that the printing is done with a rubber or more commonly plastic printing plate which is flexible as opposed to a metal plate commonly used for offset printing. Flexo printing can be done as the envelope is being manufactured or "in-line". This saves time and effort versus offset printing which is a separate process from the actual manufacture of the envelopes. There is a qualitative difference between flexo and offset. Generally speaking, for jobs that contain screens, half-tones or fine lines, offset printing is required in order to acheive the best results. Flexo printing is usually reserved for simple line copy or basic graphic images and is most commonly done for long runs of 100m or more. Flexo printing is usually less costly than offset especially on the longer runs.
-
Good question! We are a full service shop and offer a wide range of products and services. To see a full listing and description of what we can offer you, check out the Products & Services area in the Customer Service Section of our website.
-
Why are there overruns on custom jobs?
This is truly one of the more frequently asked questions in the envelope business!
Despite the suspicion by some customers that overruns represent a conspiracy among envelope companies to inflate their orders, there's actually a very simple, logical answer as to why this occurs.
Making an envelope involves several steps. The paper must be cut, the folding machine must be set up and if there's printing, a printer needs to be set up as well. There is waste involved in each of these processes. In order to ensure that the customer receives at least as many as he ordered, more envelopes need to be produced in order to allow for waste. It's virtually impossible to calculate the waste factor exactly and what usually happens is, when the job is finished, there are some envelopes left over.
Since producing this extra stock is part of the cost of ensuring the customer receives his correct count, it is customary in the industry to pass along "overs" as long as they represent a reasonable amount.
As far as what is "reasonable", most companies will say that for orders up to 5,000 there could be as much as a 25% overrun factor and it goes down from there; ie. a 50,000 order might include a 10% overrun and so forth. The larger the quantity ordered, the less a percentage of overrun is considered acceptable.
This will usually only apply to a custom size order. A standard #9 or #10 can easily be reused with another customer so there is no reason to bill for overs.
Customers can and do specify "no overs" on their PO but in that case, the cost of the waste is simply calculated into their per-thousand price for what they order so they are paying for it anyway. Some customers specify a certain percentage of what is acceptable for overs or unders on their purchase order (orders can be underrun as well but it is less common). It helps to disclose any preferences in this regard in advance so there are no misunderstandings after the fact.
-
Why do the printed colors look different from the colors on my screen?
In short, printers and monitors produce colors in different ways.
Monitors use the RGB (red, green, blue) color model, which usually supports a wider spectrum of colors. Printers use the CMYK (cyan, magenta, yellow, black) color model, which can reproduce most—but not all—of the colors in the RGB color model. Depending on the equipment used, CMYK generally matches 85–90% of the colors in the RGB model.
When a color is selected from the RGB model that is out of the range of the CMYK model, the application chooses what it thinks is the closest color that will match. Programs like Adobe Photoshop will allow you to choose which color will be replaced. Others may not.
-
What's the best way to print an envelope?
There are two main criteria for deciding how to print your envelopes: aesthetics and price – or most commonly a combination of the two.
The aesthetic or look of the piece is generally going to be determined by marketing factors; i.e. the purpose for which the envelope will be used. A simple function like letterhead or mailing an invoice will not require an elaborate look. In fact, going overboard on design for an envelope with a modest purpose might actually send the wrong message such as; “We’ve got way too much money to spend so thanks to all our customers for putting us in this position.” On the other hand if you’re selling something – a new and exciting product or service, you’re probably going to want match the excitement of the offering with the appropriate graphics and color.
Fortunately for direct marketers and small business owners, envelope companies like Elite Envelope & Graphics will generally have the capabilities to print whatever your fertile imagination can create. In a previous blog I described in detail the various ways to print an envelope. These are: lithographic (on flat sheets for converting after the fact), offset (mostly done on Halm brand Jet presses but also can be done on smaller presses like an AB Dick with special envelope feeders), flexographic (typically done in-line while an envelope is being folded) and finally, digital (either on flat sheets for converting or on newer model presses that accept pre-converted envelopes).
Each of the four envelope printing methods listed has its own unique characteristics and uses.The most common method is offset. The reason for that is because it gives the best look for the best price in most situations. An envelope can be offset printed at quantities as low as 1,000 at very reasonable prices. The Halm Jet press, which is what most envelope company’s use, is built for speed and higher volumes. Printing on a Jet press will generally become most competitive at around 5,000 pieces and up.
Offset printing is done with metal plates that allow for a sharp, clean image even with halftone screens and fine lines. The Jet Press will allow for the envelope to bleed to the edge and print fairly heavy solid coverage and can print anything from black ink up through and including four color process. All things considered, Jet Offset printing including four color Jet printing provides many options at competitive prices.
Lithographic (or litho for short) is the way to get the highest print quality when that is required. The reason for that is a combination of the method and the fact that litho presses tend to be large and sophisticated with many built-in features that allow for very fine reproductions. When an envelope is designed with full ink coverage on all sides (printers sometimes refer to this as a “paint job”) it is generally printed lithographically on flat sheets. The individual envelope impressions contained on the printed sheets are then die cut and fed into an envelope folding machine where they are scored, glued and folded into envelopes. This process is referred to as envelope converting. Lithographic printing and converting is more expensive than printing a pre-made envelope on a Jet press. However, it is necessary for certain graphic designs. One way to reduce cost for this option is to print the copy on a cold web press. These presses can print the same heavy coverage as flat sheet presses but can do so more economically. Elite Envelope & Graphics features cold web printing up to eight colors in addition to the more traditional forms of envelope printing.
Flexographic or flexo is done with hard plastic, photo-polymer plates. The impression is raised on the plate and is applied to the substrate in a similar fashion to the older and mostly out-of-date letterpress process. Flexo printing in the envelope world is almost exclusively done in-line while the envelope is being folded. Certain larger and more sophisticated envelope converting machines have flexo printing capability which allows the printing and folding to be done at the same time. This greatly reduces cost especially for large-volume print runs which is primarily where this type of printing makes sense. The high cost to set up these machines to fold and print generally makes flexo printing uneconomical at quantities of 100,000 or less. While the flexo printing technology has improved to the point where it can produce certain full-coverage items that heretofore could only be printing litho, flexo printing is not going to be as sharp and vibrant as litho or even offset printing. However, for the high-quantity runs, even for four color process, flexo printing can be an excellent option for an envelope.
Lastly, digital printing has made inroads into the envelope market over the past ten years or so. Printing digitally with toner rather than ink can yield good results depending on a few factors. First, it can only be done with process colors, not spot colors. Any art file can be converted from spot colors to process but if a company’s logo is to be printed in a certain, specific PMS color, converting to process may not yield an exact match to the PMS chart. Secondly, digital presses are best suited for small quantities. Printing in general will show lower unit costs as the quantity of a job increases. This is mostly because the set-up of a job is a significant cost that is the same to print 500 pieces as it is to print 500,000. The longer the print run, the more the set up cost can be amortized which allows the unit cost to decrease. The same principle however doesn’t apply to digital printing. There is no comparable set-up cost to a digital print job. It’s similar to printing something from your desktop computer. Once the file is ready to go, you press “print” and you’re off and running. Digital printing is generally priced at a “click charge” or per piece charge. Eliminating the set up cost allows for lower quantity jobs to be relatively inexpensive but since there’s nothing to amortize, the same price applies to every piece in the run. This makes digital envelope printing competitive for quantities up to around 2,500 pieces. After that, you’re better off going offset.
One last benefit of digital printing is if you need variable data on the envelope. Some small mailings can be addressed digitally. Or you can vary your teaser copy or code numbers more easily through digital printing. Elite Envelope and Graphics is one of a few companies that can take digitally printed sheets with variable data and convert them into envelopes.