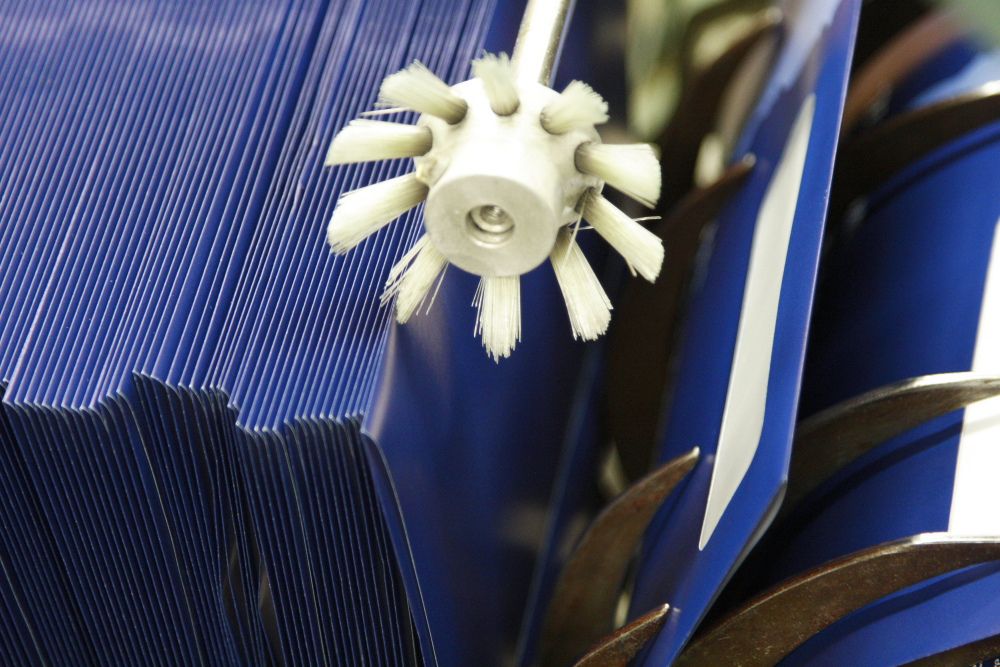
The term “converting” in relation to envelopes is sometimes not well-understood. So, here’s a very simple definition: Envelope converting is the process by which sheets of paper are cut, glued and folded into envelopes. An envelope converter is a company that has the machinery and personnel to do this. An envelope converter is the same thing as an envelope manufacturer. It’s a factory where envelopes are made. To “convert” means to change. We envelope converters are “changing” paper into envelopes; hence the name.
An envelope conversion starts with sheets or rolls of paper. The paper can be unprinted, covered with ink on both sides or anything in between. In either case the process is the same with a few modifications depending on the paper and whether or how it is printed.
Let’s take a simple, hypothetical order and go through it step by step to illustrate the process.
“ABC Printing” has a customer who wants 5,000, 24# white wove, #10 standard window envelopes with full printing coverage on all sides. Since the envelope is easily available as a stock item, ABC is wondering if Elite Envelope can simply print on the stock envelope. This isn’t possible for two reasons: first, envelope presses cannot print full ink coverage on two sides of an envelope. For starters, there would be ink build-up, seam markings, ink rub-off and that’s assuming that the presses could even be set up to do it. Second, because the customer wants the printing to bleed right to edge of the window all around, it’s impossible to print this without hitting the window occasionally.
This is a perfect example of an envelope job which must be converted. ABC Printing has the capability to print up to a 19 x 25 sheet size. Elite Envelope will supply them with a digital file showing the outline of the unfolded envelopes (called “blanks” in the envelope biz) set up in the proper position for printing. In this case, 4 envelopes can be printed on this sheet. The diagram which shows how the envelopes must be placed on the sheet for proper conversion is called a layout. The printer must set the job up in the exact manner specified by the layout.
Once the printer sets up his artwork on the layout sheet, he will send a sample sheet to the envelope converter for final approval before printing. The converter will inspect to make sure that the sheet matches the layout in all respects and, if so, will tell the printer the job is ready to print.
Because there is waste involved in the envelope converting process, ABC has been advised to include a certain amount of extra sheets. The smaller the order, the higher the percentage of extra sheets is required. Also, jobs that have windows or on glossy paper will require higher amounts of waste sheets. In addition to the regular printing sheets, they will also supply what are called “spotter sheets” which are regular press sheets with dots added in the 4 main corners of the envelope. The cutter will place the die exactly on the spots on the sheet to ensure a consistent and accurate cut.
The printer will print the job and stack the sheets on a pallet making sure that the edges are jogged so that the sheets line up perfectly on top of one another. This is an important step taken to ensure uniformity in the cutting process. The printer will take care to pack the sheets on the pallet and strap them tightly so they don’t move in transit.
At this point, the envelope converter takes over. We’ll continue in the next blog post. In the meantime, if you’d like more information on envelope converting, custom envelope manufacturing or envelope printing for that matter, just go to www.eliteenvelope.com .